Description
Tri-Pak vertical balers are available in a wide range of sizes and capacities ranging from the TB-4527 series that produces a 100 pound bale to the TB-7230 series that can produce 2,000 pound bales. Every baler meets/exceeds the latest ANSIZ245-2013 specifications as well as the current OSHA, CSA, UL and MOL electrical and guarding regulations. Dual safety circuits are standard as are tamper resistant coded magnet safety sensors. Every baler is equipped with a chain free bale ejection system that is engaged from the front of the baler and uses the baler’s own cylinder to automatically eject the finished bale out of the bale chamber. The PLC based control panel alerts the operator via a “bale full” light when a full bale condition has been achieved. There is no longer any need for the operator to visually check to see how full the baling chamber is getting. Every baler can be upgrades with rear wire guides, bale counters, front door tie slots and a SCADA based baler monitoring system that is able to monitor all of the balers systems to reduce down time and gray area service calls.
Technical Details
Standard Features
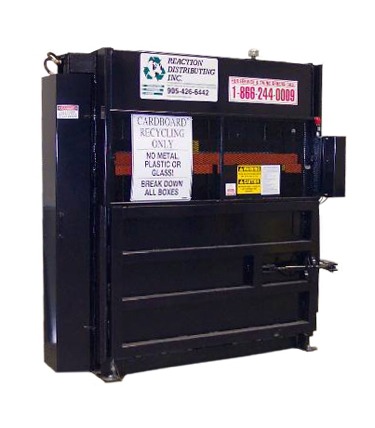
- UL/CSA Approved Design
- Meets/exceeds ANSI Z245.2 regulations
- Meets/exceeds OSHA regulations
- PLC “flex-design” based control systems
- NEMA 4 rated enclosure
- Internal timers prevent system run-on
- Self-diagnostic indicators
- 24-volt controls
- Adjustable multi-cycle timer
- 75% and 100% full light
- Auto-alert maintenance mode
- Heavy duty oil-tight pushbutton controls
- Key lockable start pushbutton
Mechanical Specifications
7230 | 7230HD | 7242 | |
---|---|---|---|
Bale Size | 72″x 42″ x 30″ | 72″x 42″ x 30″ | 72″x 42″ x 42″ |
Bale Weight | +1200 lbs | +1200 lbs | +1500 lbs |
Cylinder Size | 2 x 5″O | 2 x 5″O | 2 x 5″O |
Full Penetration Cylinder | NO | NO | NO |
Baling Force Normal | 78,500 lbs | 78,500 lbs | 78,500 lbs |
Baling Force Maximum | 86,350 lbs | 86,350 lbs | 86,350 lbs |
System Pressure Normal | 2,000 psi | 2,000 psi | 2,000 psi |
System Pressure Maximum | 2,200 psi | 2,200 psi | 2,200 psi |
Cycle Time | 45 seconds | 40 seconds | 40 seconds |
Pump Capacity | 15 gpm | 20 gpm | 20 gpm |
Motor Size | 15 hp | 20 hp | 20 hp |
Platen Pressure Normal | 36.0 psi | 36.0 psi | 26.0 psi |
Platen Pressure Maximum | 43.0 psi | 43.0 psi | 31.0 psi |
Oil Tank Capacity | 25 gal | 25 gal | 25 gal |
Bale Ejection | Dual chain | Dual chain | Dual chain |
Shipping Weight | 5200 lbs | 5200 lbs | 6025 lbs |
Electrical Specifications
Control System | 110 volt 60 cycle powered by step-down transformer |
Control Panel | Fully wired. Keyed start button, emergency stop, full lights, reset button |
Power | 208/230/575 volt, 3 phase 60 cycle |
Dimensions
A | B | C | D | E | |
---|---|---|---|---|---|
7230 | 90″ | 100″ | 42″ | 48″ | 23″ |
7230HD | 90″ | 100″ | 42″ | 48″ | 23″ |
7242 | 90″ | 100″ | 54″ | 48″ | 23″ |
Optional Equipment
- Deep Chamber (42″)
- Full bale light
- Hydraulic bale dump
- R.H. hinged bale door
- Barn style feed doors
- Rear wire guides
Electrical system upgrades
- System monitor: SCADA panel (add-on panel or integrated upgrade) provides cell-based monitoring of all systems including container fullness, safety circuit devices, container positioning, hydraulic system devices including reservoir fullness, oil temperature and system in-use time
- Remote start/stop station
- Auto-start system (photo-eye or sonic sensor)
- Wireless remote control
- Biometric interface
- HMI based operator interface for tie into building monitoring systems
Hydraulic system upgrades
- Single phase and three phase power units
- Hi-lo hydraulic pumps for reduced cycle time applications
- Regen circuit for improved hydraulic fluid circulation
- Over-sized oil reservoirs to accommodate ancillary devices and improved heat sink
- Oil cooler for high duty cycle applications
- Bio-degradable oil
- In tank oil heater
- Sonic sensors for oil fullness monitoring
- Low temperature oil (as low as -60 Celsius is available)
Compactor upgrades
- Custom chute systems
- Custom weather enclosures
- Drive-on deck systems (certified up to 20,000 lbs.)
- Tongue and grooved floor designs
- AR plate floors and sides for reduced press head/compactor shell wear
- Pad-less set-up for installation on asphalt
- Custom hydraulic cart tipping systems
- Light curtain-based safety sensors
- Custom steel safety barriers
- Custom hydraulic lift systems